LES CANNES À MOUCHE de DANIEL BRÉMOND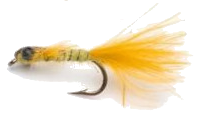
Accueil | Genèse | Structure alvéolaire | Assemblage par épissures | Études de profils | Résultats théoriques | Souvenirs | Contact |
Accueil | Genèse | Structure alvéolaire | Assemblage par épissures | Études de profils | Résultats théoriques | Souvenirs | Contact |
Les résultats rappelés dans ce chapitre sont à la base de mes recherches dans le but d’améliorer le fonctionnement des cannes à mouche qui ont abouti à la structure alvéolaire, à l'assemblage en épissure et à mes méthodes de calcul de profils. Ils relèvent des domaines de la mécanique des solides et de la résistance des matériaux et utilisent des outils mathématiques seulement abordés en fin d’études secondaires : le calcul vectoriel et le calcul intégral.
Que faire pour qu’ils ne soient pas trop hermétiques si on ne les maîtrise pas ?
Je propose de retenir les résultats exprimés en caractères gras et, seulement si besoin, de lire le détail de mes explications. Je peux aussi répondre à des questions.
L’aire d’un hexagone régulier peut s’exprimer par rapport à différentes longueurs : celle de son coté, ou du rayon du cercle circonscrit, ou de celui du cercle inscrit qui s’appelle aussi l’apothème. La cote sur plats \(C\) est directement visible et mesurable.
\(A=C \times \sqrt{3} \times \dfrac{C}{2}\) \(A=\dfrac{C² \times \sqrt{3}}{2}\)
Si l’on respecte les unités “officielles”, \(C\) est en mètre et l’aire en m². Mais rien n’interdit d’utiliser un sous multiple, par exemple le mm² pour nos cannes à mouche.
Evidemment, si l’hexagone est creux, \(C’\) est la cote sur plats de l’hexagone intérieur,
$$A=\left(C^2-C'^2\right) \dfrac{\sqrt{3}}{2}$$
La cote sur plats n’existe, il va de soi, que si le nombre de cotés est pair ! Si l’on veut une expression générale, il faut choisir une autre longueur de référence, par exemple l’apothème.
Si a est l’apothème, n le nombre de cotés, pair ou impair,
$$A=na^2 \times tan \dfrac{180}{n}$$
L’usinage des six baguettes triangulaires qui vont constituer la section hexagonale nécessite le respect du profil choisi donc le respect de la cote sur plats \(C\) définie point par point et le moyen de la vérifier.
Comme beaucoup de constructeurs avant moi, j’ai eu l’idée de donner le profil des baguettes en les logeant dans une rainure entre deux règles en acier d’écartement variable. Ce qui permet de les raboter jusqu’à ce qu’elles affleurent au plan supérieur des règles. Sur la vue en coupe ci-dessous les sections des règles sont hachurées, celle de la baguette à la fin du rabotage occupera le triangle équilatéral \(ABS\). La question est de régler sa hauteur qui correspondra à la demi-cote sur plats de l’hexagone complet notée \(\dfrac{C}{2}\) en jouant sur l’écartement des règles. Ce qui nécessite de pouvoir la mesurer alors que le point \(S\) que j’ai tracé est dans le vide, non matérialisé. Deux méthodes possibles : une très classique, dans laquelle on loge un cylindre rectifié de rayon connu : la pige. La “cote sur pige” \(C_p\) est mesurée entre les faces inférieures des règles et la tangente à la pige avec un pied à coulisse ou un micromètre (palmer). L’autre méthode consiste à loger une cale triangulaire de hauteur précise dans la rainure et de déduire sa profondeur du dépassement de la cale.
Cotes sur pige :
On calcule de combien la pige dépasse de la face supérieure des règles par la différence entre la cote sur pige et l’épaisseur des règles : \(d = C_p-e\). Puis \(\dfrac{C}{2} = HS = TS-d = 3r-d \) soit \(\dfrac{C}{2} = 3r-d\)
Exemple : \(r=2\) mm \(e = 14,5\) mm \(C_p = 15,60\) mm \(d = 15,6 - 14,5 = 1,1\) mm
\(\dfrac{C}{2} = 3r-d = 3 \times 2 -1,1\)\(\dfrac{C}{2}=4,9\) mm
Parce que le calcul est un peu plus compliqué quand l’angle \(\widehat{ASB}\) prend une valeur quelconque, différente de 60°, les calculs de cotes sur piges sont un pont aux ânes pour les apprentis mécaniciens : on pige ou pas ! La valeur 14,5 mm de l’épaisseur des règles est celle de la majorité des miennes, en acier profilé. Comme piges, j’utilisais les queues de forets à métaux.
Mesure avec une cale triangulaire :
La mesure avec une pige présente l’inconvénient d’un contact linéaire entre elle et les flancs de la rainure qui peuvent présenter des irrégularités. D’où l’idée de disposer d’une cale dont la section est un triangle équilatéral qui va se loger dans la rainure flanc contre flanc, de la même façon que les baguettes que l'on doit tailler. On procède comme précédemment en mesurant cette fois la “cote sur cale”. Si \(h\) est la hauteur de la cale, une cote virtuelle car on ne peut faire une mesure sur un angle, \(d\) son dépassement, la profondeur de la rainure vaut \(h-d\) au lieu de \(3r-d\).
On a donc \(\dfrac{C}{2} = h-d\)
C’est mon collègue B.D. qui avait eu l’idée de cette cale en acier trempé qu’il avait usinée avec beaucoup de précision, avec une tolérance inférieure au centième de mm. Il avait choisi 5 mm de hauteur.
Il est aussi à l’origine de deux autres cales aux profils femelles qui permettent de mesurer non pas le logement des baguettes mais les baguettes elles mêmes, même si l’angle intérieur est rabattu.
Mesure des baguettes avec des cales rainurées.
De même il n’y a pas moyen de mesurer la cote \(\dfrac{C}{2}\) sur une baguette en cours de taillage, à fortiori quand les alvéoles sont amorcées.
Mon collègue B.D. a résolu le problème avec deux cales rainurées (voir photo, et schéma ci-dessous).
L’une et l’autre mesurent 15 mm de large et 25 mm de longueur. Leurs faces horizontales sont rectifiées, seule la face inférieure est fonctionnelle, usinée de telle façon que l’apex de la rainure à 60°, noté S dans les schémas, soit à exactement 5 mm de cette face. S est un point virtuel, le fond “théorique” de la rainure, et il convient de rabattre l’arête interne des baguettes pour qu’elles se logent parfaitement dans la rainure.
L’une de ces cales a une épaisseur de 7,2 mm. Elle permet donc de mesurer les hauteurs des sections en triangle équilatéral au dessus à de 2,2 mm. (7,2 mm - 5 mm). Elle est adaptée aux baguettes de talon.
L’autre pour les baguettes de scion a une épaisseur de 6,2 mm permet les mesures à partir de 1,2 mm (6,2 mm - 5 mm).
Sur chacune B.D. avait gravé “5” pour rappeler qu’il faut soustraire 5 mm à la cote mesurée entre la face inférieure de la cale et la face supérieure de la baguette.
Si on ne dispose pas de telles cales, le seul recours pour vérifier la cote sur plats de la section hexagonale en un point donné c’est d’usiner 6 petits morceaux de baguettes, de les assembler pour constituer un court tronçon hexagonal servant de témoin et de mesurer C. C’est pour le moins laborieux !
Le moment quadratique de la section d’une tige (pour nous une canne à mouche !) est la grandeur géométrique qui caractérise sa résistance à la flexion ou, si l’on veut, sa raideur, l’autre grandeur physique étant le module de Young qui dépend du matériau.
Pour une section quelconque, le moment quadratique dépend de la direction de la flexion. C’est le cas par exemple pour une canne en fibre quand le centre du cercle intérieur ne coïncide pas avec le centre du cercle extérieur. Si on la fait pivoter une fois courbée, on ressent dans deux sens de flexion opposés que la canne résiste moins et, dans une direction perpendiculaire, qu’elle résiste plus dans les deux autres sens opposés. Un exemple : si la canne est plus souple quand on la plie dans un plan horizontal tant vers la gauche que vers la droite elle sera plus raide dans le plan vertical tant vers le haut que vers le bas. (Ne pas confondre sens et direction au sens mathématique : la verticale est une direction à laquelle on associe deux sens opposés : vers le haut ou vers le bas.)
Pour tous les polygones réguliers, le moment quadratique est indépendant de la direction et du sens de déformation. On ne ressent ni point dur ni point faible en torsion. C’est déjà vrai si la section est un triangle équilatéral (le cas général d’un moment quadratique variable suivant la direction de flexion sera traité plus loin.)
Pour une section hexagonale si \(Q\) est le moment quadratique, toujours en fonction de la cote sur plats :
\(Q=\dfrac{5C^4 \sqrt{3}}{144}\) |
Mêmes remarques que pour l'aire :
a) l’unité normalisée est le \(m⁴\) mais pour les cannes à mouche le \(mm⁴\) s’impose.
b) Une expression générale de \(Q\) pour un polygone régulier en fonction de l’apothème \(a\) :
\(Q=\dfrac{a⁴ \times n}{12}\left[3tan \dfrac{180}{n}+tan³ \dfrac{180}{n}\right]\) |
Ou, si les angles sont mesurés en radian :
\(Q=\dfrac{a⁴ \times n}{12}\left[3tan \dfrac{\pi}{n}+tan³ \dfrac{\pi}{n}\right]\) |
Cette formule générale permet de retrouver le moment quadratique d’un disque, en faisant tendre \(n\) vers l’infini. Dans ce cas, l’expression entre crochets tend vers \(\dfrac{3}{n} \pi\) , l’apothème se confond avec le rayon et donc \(Q\) tend vers \(\dfrac{\pi}{4}r⁴\)
\(Q_{disque}=\dfrac{\pi}{4}r⁴\)
Cette raideur qui dépend de la puissance quatre d’une longueur fait qu’elle est comme dissimulée à notre regard, et qu’une majorité d’entre nous n’en a même pas l’idée !
Nous y reviendrons longuement dans le chapitre « Études de profils », mais déjà deux exemples pour ressentir cette grandeur :
Si la cote sur plats est doublée, la raideur est 16 fois plus grande.
Si on augmente la cote sur plats dans une petite proportion, par exemple de 1 % la raideur \(Q\) augmente de 4 %.
Cas d’une section hexagonale creuse : même formule mais avec \((C⁴ - C’⁴ )\) à la place de \(C⁴\). La question sera développée au chapitre « Structure alvéolaire ».
J’insiste sur “refendu” et qui plus est, pour mes cannes, refendu alvéolaire. Donc un matériau dans lequel toutes les zones moins denses, moins concentrées en fibres ont été supprimées. C’est vraiment le meilleur qui reste ! Donc il n’est pas étonnant de trouver une valeur largement supérieure à la valeur usuelle de 20 gigapascal qui correspond aux troncs bruts, sachant que, pour un matériau élastique, plus le module de Young est grand moins il faut de matière pour résister aux déformations.
Le module de Young conditionne la sonorité d’un bois ou autre matériau quand on le choque : plus elle est aiguë meilleur il est !
Comment peut-on le calculer ? En pliant la canne.
En un point P de la canne on exerce un moment de flexions \(MtF\), \(C\) est la courbure en \(P (C=1/R, R\) étant le rayon de courbure en m). \(Q\) est le moment quadratique en \(P\) qui est la grandeur géométrique qui conditionne la résistance à la flexion (la raideur) de la canne. On a :
\(MtF=C \times Q \times Y\) |
Il est intéressant de mettre en parallèle cette relation avec celle qui relie l’allongement relatif \(dL/L\) d’une tige dont la section a une aire \(S\), quand elle est soumise à une force \(F\) :
$$F=dL/L \times S \times Y$$
Pour l’allongement c’est le produit de l’aire \(S\) de la section par le module de Young qui résiste à la force. Pour la flexion c’est le produit du moment quadratique \(Q\) de la section par le module de Young qui résiste au moment fléchissant. Le module de Young présent dans les deux relations caractérise la résistance du matériau aux modifications de longueur des fibres.
Ceci étant, la relation encadrée permet d’exprimer \(Y Y=\dfrac{MtF}{CQ} \). Après plusieurs mesures, qui ont consisté à faire coïncider la courbure de la canne avec des courbures déjà tracées, le moment fléchissant étant connu de même que la cote sur plats, j’ai obtenu une valeur du module de Young supérieure à 45 gigapascals \(Y\geq45 \times 10⁹Pa\), soit plus du double de celui du bambou brut.
Les bambous que j’ai utilisés provenaient, dans leur grande majorité, de Pezon & Michel, avec une assez grande dispersion dans les diamètres des troncs. Un grand diamètre n’est pas synonyme de qualité.
Mais j’en ai reçu d’autres.
De Jean Michel DUBOS qui m’avait offert un jeu de baguettes qu’il avait taillées dans un bambou très clair, NON trempé (voir plus loin trempe du bambou).
De Tim BEDFORD, un jeu de baguettes puis des troncs.
De Walter BRUNNER, un jeu de baguettes qui m’a permis d’assembler une « Pielach » alvéolaire en juillet 74. 2,44 m 100 g.
Du danois Preben Torp JACOBSEN, des troncs. Je lui ai fabriqué une canne.
En qualité, les baguettes de Tim BEDFORD étaient incomparables, sans doute issues du stock de bambous de DICKERSON (Tim n’avait commencé à fabriquer des cannes qu’une fois en retraite et avait racheté tout le matériel de cet artisan américain), suivies par celles de Walter BRUNNER.
La qualité du bambou est difficile à évaluer avant de le travailler, et même avant de tester le produit fini. Le diamètre des troncs, l’épaisseur de la couche des fibres les plus dures ne sont pas déterminants. Seul l’est le module de Young mais encore faut-il le mesurer. Le son plus ou moins aigu à la percussion est un bon indice.
Cela me donne l’occasion de revenir sur la parenté et les différences entre la méthode d’allègement astucieuse des POWELL père et fils et la mienne.
E. C. POWELL avait remarqué la qualité particulière de certains bambous qui possèdent une couronne étroite de fibres dures rassemblées à la périphérie du tronc : « A thin ring of very dense fibers ». Ce qui prouve qu’il avait compris, à défaut de s’appuyer sur des résultats théoriques, le rôle primordial des fibres extérieures.
D’où l’idée de reconstituer artificiellement cette structure en supprimant les fibres intérieures inutiles qu’il remplaçait par un bois plus léger (brevet déposé en 1931 !). J’ai trouvé des indications dans « Classic Rods and Rodmakers » p. 176 sur les épaisseurs de bambou conservées allant de 70/1000 inch soit 1,8 mm mais pouvant descendre à 50/1000 inch soit 1,27 mm de ces « laminated rod » ! Si j’avais pu me procurer des feuilles minces constituées de fibres de carbone alignées et non croisées, j’aurais tenté de compléter leur épaisseur par une mousse plus ou moins dense et de tailler des baguettes triangulaires dans ce matériau composite !
Pourquoi E.C. POWELL et son fils n’ont pas à ma connaissance été les initiateurs de la structure alvéolaire ? Deux raisons à mon avis : la qualité des colles insuffisante dans les années 30 au vu de la petite surface de contact et les impératifs de la production en grand nombre (750 par an) qui les empêchait de tenir compte baguette par baguette de l’emplacement des nœuds.
Les Anglo-saxons baptisent leur technique « semi hollow built rod » qui en l’occurrence est plutôt semi-pleine que creuse. En cherchant sur le net j’ai trouvé deux fabricants : « Kretchman Bamboo, Fly Rod Models » et « Brandin slip-cane rod » qui y font référence. Ce dernier présente d’une façon poétique une de ses premières cannes en coupe : « One of my earliest semi-hollow efforts completed in 1989, cut open to show the internal structure, including what I call my "internal swell." » (La succession des points d’appuis est comparée à des vagues internes !).
La photo qu’il présente est exactement la structure alvéolaire avec une belle proportion d’évidement et des cloisons peu espacées. A voir !
La “trempe” du bambou.
Bien qu'utilisé pour l'acier ou le verre, le terme de “trempe” peut s'appliquer aussi au bambou, le but étant le même : modifier les caractéristiques mécaniques d'un matériau.
La trempe de l'acier améliore la dureté, la limite élastique, la résistance maximale, le module de Young. Pour le verre, elle améliore la résistance mécanique.
De la même façon, la “trempe” du bambou modifie ses caractéristiques en améliorant considérablement le module de Young.
Une expérience significative et simple à réaliser consiste à plier en arc une baguette de bambou “crue” et à observer, dans un premier temps, que sa courbure est maximum en son milieu.
Puis on promène les 15 à 20 cm de la partie centrale qui a le plus fléchi au-dessus de la flamme d’une lampe à alcool jusqu’à un léger noircissement des angles. Après refroidissement on plie de nouveau la baguette. On a alors la surprise de constater que la partie “cuite” qui est pourtant soumises aux plus fortes contraintes puisque située au milieu, résiste résolument à la flexion ! Voilà les courbes qu’on obtient :
C’est parlant et tous ceux à qui j’ai montré cette petite manipulation ont été convaincus de l’effet largement bénéfique de la cuisson.
Mais comme on ne peut en déduire un pourcentage d’augmentation du module de Young, je viens de réaliser l’expérience suivante :
Le matériel se compose d’une baguette brute, seulement sortie d'un tronc, dont j’ai un peu réduit l’épaisseur pour éliminer la zone où les fibres sont rares, crue, c’est important d’en être sûr[1]Note [1] – Devrait correspondre à la question du bambou tel qu'on le reçoit. A-t-il ou non été chauffé ? et pour cela j’ai soigneusement observé mes réserves pour le choix de l’éprouvette, d’un tube d’alu (1 m) qui va servir de bras de levier, d’une bouteille plastique que l’on leste avec de l’eau et d’un serre-joint.
On fixe la baguette sur un support horizontal[2]Note [2] – C'est un détail technique : il me semble que c'est mieux de fixer l'éprouvette légèrement ascendante plutôt qu'horizontale. en laissant dépasser une vingtaine de centimètres. On l’enfile dans le tube alu en laissant une partie libre de quelques centimètres (cette longueur qui va plier doit être repérée avec précision). On accroche la bouteille (250 g...) à l’extrémité du tube. Le tronçon de bambou entre le serre-joint et le tube se plie. On mesure la flèche \(F_1\) en bout de tube.
On démonte et on chauffe la partie qui a été fléchie puis on recommence et on mesure \(F_2\).
Je viens de faire l’expérience avec un chauffage modéré qui a carbonisé les angles mais sans modifier sensiblement la nuance de l’émail. J’ai obtenu \(F_1 = 21,6 cm\) et \(F_2= 18 cm\). Ce qui correspond à un augmentation du module de Young de 20 %.
C’est déjà beaucoup plus que ce que j’ai pu lire et je suis persuadé qu’on peut faire mieux. Comment expliquer cette divergence ? Je n’ai pour l’instant qu’une seule hypothèse : est-ce que bon nombre de troncs n’ont pas étés étuvés avant d’être expédiés ?
J’espère que cette expérience “primitive”, avec les moyens du bord, sera reprise et que les résultats pourront être comparés. Les précautions sont de bien préciser la longueur fléchie, qui doit être inférieure à 10 cm, sans être trop courte car alors les flèches diminuent et l’erreur relative de leurs mesures augmente. Le support sur lequel on fixe la baguette gagnerait à avoir une pente (de l’ordre de 30°)qui l’oriente vers le haut.
Reste à expliquer l’effet de la chauffe. Certes elle élimine l’humidité résiduelle mais l’amélioration des qualités mécaniques ne s’observe que quand on atteint un seuil proche de 200°C alors qu’un chauffage prolongé à 140°C, par exemple, l’éliminerait tout autant sans améliorer le matériau. C’est pourquoi je penche pour une transformation chimique.
Un dernier avantage et non des moindres de la cuisson : les bambous crus ne se comportent pas comme un matériau élastique. Une fois courbés, ils gardent une flexion rémanente. J’en avais discuté avec Jean Michel DUBOS qui ne s’inquiétait pas que ses cannes restent courbées après la capture d’un poisson. Les baguettes qu’il avait taillées et qu’il m’a offertes sont très très claires, elles n’ont pas connu le four. C’est une option. Alors que le bambou cuit répond à la définition d’un matériau élastique avec des déformations réversibles : après différents efforts, la canne au repos retrouve sa rectitude... toutefois si les contraintes restent modérées. C’est d’ailleurs un critère de bon usage.
Durabilité : après plusieurs dizaines d’années aucune des cannes que j’ai achetées ou que j’ai fabriquées n’ont perdu cette propriété.
Je m’interroge sur la reprise d’humidité. J’ai décollé en les plongeant dans l’eau pas mal de sections anciennes en bambou refendu. Il me semble, je n’irai pas plus loin, que les sections séchées sans les chauffer et recollées avaient gardé cette qualité.
On considère une force \(\overrightarrow{F}\) d’intensité \(F\) (en newton N) qui s’exerce dans l’axe d’une tige ou d’un fil de longueur \(L\), de section \(S\) (aire en coupe en m²). Elle va provoquer une variation de longueur (allongement ou tassement) jusqu’à ce que les fibres étirées ou tassées exercent une force qui équilibre \(\overrightarrow{F}\). On note \(dL\) la variation de longueur et \(dL/L\) l’allongement relatif. Exemple : si une tige de longueur 10 cm s’allonge de 1/10 de mm soit 0,01 cm, son allongement relatif est 0,01/10 = 1/1000 ou 10-3 (sans unité).
Pour des petites déformations, réversibles, \(F = dL/L.S.Y\) ou
Relation (R1) \( \displaystyle \frac {dL} {L} = \frac{F} {S \times Y}\)
\(F\) en newton, \(S\) en m², \(dL\) et \(L\) dans la même unité de longueur. \(Y\) est le module de Young qui caractérise la résistance à la déformation du matériau. Son unité N/m² s’appelle le Pascal Pa (unité internationale de pression).
On comprend que, plus la section est grande, ainsi que le module de Young, moins la tige se déforme.
Le produit \(S.Y\) caractérise la résistance de la tige aux modifications en longueur, ou module d’élasticité.
Il faut retenir que la déformation relative en longueur est proportionnelle à l’intensité de la force qui la provoque et inversement proportionnelle à la section.
Exemple :
Calcul de l’intensité \(F\) de la force nécessaire pour allonger une fine tige en chêne de 0,8 m de long, de section s = 16 mm² (soit 16x10-6 m²) de 0,1 mm soit 0,0001 m.
Le module de Young du chêne est 12 x 109 Pa (celui du bambou est nettement supérieur, on le verra plus loin).
L'allongement relatif \(dL/L\) est 0,0001/0,8 soit 0,000125 que l'on écrit 1,25 x 10-4
$$F = 16 \times 10^{-6} \times 1,25 \times 10^{-4} \times 12 \times 10^{9} \;\;= 240 \times 10^{-1} \;\;\;\; F = 24N$$
Ces résultats trouveront leur application au paragraphe suivant 7) Résistance à la flexion.
Contrainte des fibres. C'est le quotient \(\large\frac{F} {S }\) en N/m²
On a \({\large\frac{F} {S}} = dL/L \times Y\). La contrainte est proportionnelle à l'allongement relatif.
On considère une baguette en bois, ou autre matériau souple et léger (pour pouvoir négliger la pesanteur) homogène, rectiligne. L’axe de cette tige est une droite \(Dg\) qui passe par les centres de gravités des sections.
Si en un point A de la tige on applique une force, elle va produire en un point M de \(Dg\) un moment de flexion \(MtF/M\) ; sommairement on a \(MtF/M = F \times L\), \(F\) intensité de la force en newton, \(L\) bras de levier en mètre. D’une façon rigoureuse le moment de flexion est un vecteur \(\overrightarrow{MtF/M}\), produit vectoriel du vecteur “bras de levier” \(\overrightarrow{MA}\) par \(\overrightarrow{F}\). Ce moment va provoquer une courbure de la tige, donc un allongement ou tassement des fibres, donnant naissance à des forces selon les résultats vus au 1), produisant un moment de résistance à la flexion \(\overrightarrow{MtR/M}\). L’équilibre est atteint quand la somme de ces vecteurs est nulle.
Au point M, il existe un cercle qui vient s’ajuster à la courbe de \(Dg\) (voir schéma), on l’appelle le cercle osculateur, son rayon est le rayon de courbure \(R\) de la tige en ce point.
Plus le moment de flexion est grand plus la tige est courbée et plus \(R\) est petit !
Aussi il est intéressant d’introduire son inverse : la courbure \(C = 1/R\).
De même qu’au paragraphe 5) où l'on avait une proportionnalité entre l’allongement relatif et \(F\), on aura une proportionnalité entre le moment fléchissant et la courbure.
Il reste à trouver en flexion l’équivalent du rôle joué par la section dans la résistance aux élongations.
Exemple de calcul pour une section rectangulaire :
Dans ce schéma le moment de flexion qui est la cause de la déformation est le vecteur MtF/M qui va du point M à la pointe de la flèche de droite. Le moment résistant MtR/M est celui qui va de M à la flèche gauche. À l'équilibre, la somme de ces deux vecteurs est nulle.
Sur cette vue en coupe de la section de la tige au point \(M\), la force qui cause les déformations (non représentée) est verticale, vers le bas. Son moment de flexion au point \(M\) est représenté par le vecteur \( \normalsize \overrightarrow{MtF/M}\). Alors que la force est verticale, le plan de déformation également, ce vecteur est horizontal, d’origine \(M\), aligné avec la fibre neutre ou axe de la déformation, orienté vers la droite. C’est une conséquence du fait qu’il est le résultat d’un produit vectoriel.
Expliquons comment la section résiste à ce moment de flexion.
Pour cela, on va être amené à faire une somme de petites variations des grandeurs dites variations élémentaires. Cela relève dans le domaine mathématique du “calcul intégral”.
La longueur des fibres du segment horizontal passant par \(M\) n’est pas modifiée. Ce sont les “fibres neutres”. Celles de la partie au dessus des fibres neutres sont étirées, celles au dessous sont comprimées et réagissent à cette déformation selon la relation \(R_1\).
On considère une bande horizontale étroite de longueur \(B\), de largeur \(dx\) (hachurée sur le schéma), considérée comme un élément de section noté \(dS.\;\) \(dS= B.dx\).
Son allongement relatif est le produit de la courbure par son éloignement de la fibre neutre \(x.\) \(\;dL/L = C \times x\;\) (sera justifié plus loin)
La résistance à cet étirement est d’après \(R_1\) une force élémentaire d’intensité \(dF = C \times x.dS.Y\)
Cet élément de force va produire en \(M\) un élément de moment résistant dans la même direction que le moment fléchissant mais de sens opposé, d’intensité égale au produit de \(dF\) par \(x\), distance à la fibre neutre (bras de levier) donc : \(dMtR= C \times x.dS.Y.x= C \times X^2.dS.Y\)
(Il est intéressant de remarquer que \(x\) intervient au carré)
Pour trouver l’intensité du moment résistant total il faut faire la somme de ces moments élémentaires, \(x\) variant de zéro à \(c/2\) (calcul intégral) puis la doubler pour tenir compte de la contribution des fibres au dessous des fibres neutres qui sont comprimées.
En faisant apparaître \(B\) dans le calcul de \(dS\), on obtient \(MtR/M = C \times B \times c^3/ 12 \times y \;\) (je rappelle que \(B\) est la longueur du coté parallèle à l’axe de la déformation).
L’équilibre est atteint quand les deux intensités des moments de flexion et résistant sont égales :
\(MtR/M = C \times B \times c^3/ 12 \times y\) (c’est la relation \(R_2\)). Le terme \(B \times c^3/ 12\) s’appelle le moment quadratique ou moment d’inertie de la section par rapport à une flexion d’axe parallèle à B donc verticale et vers le bas *.
Il est intéressant de rapprocher \(R_1\) et \(R_2\)
\(\textcolor{red}{F}= \textcolor{blue}{dl/L}.\textcolor{red}{S}.Y\)
\(\textcolor{red}{MtF/M} = \textcolor{blue}{C} \times \textcolor{red}{B} \times \textcolor{red}{C^3/ 12} \times Y\)
Les premiers termes sont les causes des déformations.
L’allongement relatif dans \(R_1\) correspond à la courbure dans \(R_2\).
Enfin, le coefficient de résistance (indépendamment du module de Young) est la section \(S\) en m² dans \(R_1\) et le moment quadratique \(Q\) en m⁴ dans \(R_2\). (du fait du produit \(B\) en m et \(C^3\) en m³).
Le moment quadratique \(Q\) (ou moment d’inertie \(I\)) est une grandeur qui dépend des dimensions, de la forme de la section de la tige, et de la direction et du sens de la déformation*.
La puissance 4 d’une longueur peut surprendre. On verra plus loin ses conséquences.
La relation \(R_2\) peut aussi s’écrire \(C = \large \frac{MtF/M} {Q \times Y}\)
Le produit \(Q \times Y\)caractérise la résistance à la flexion de la tige.
Il faut retenir que la courbure \(C\) est proportionnelle au moment de flexion et inversement proportionnelle au moment quadratique de la section.
Comment représenter le moment quadratique d’une section qui dépend de sa forme, de la direction et du sens de la flexion* ?
Exemple contraire d’une section rectangulaire :
La section \(S\) est rectangulaire, de largeur \(l\), de longueur \(L= l\sqrt{2}\). On fixe la baguette de façon à ce que les deux grands côtés soient horizontaux. Le centre de gravité \(G\) de \(S\) est l’intersection de ses diagonales. Il est assez évident que cette baguette aura une plus grande résistance aux flexions dans un plan horizontal (gauche ou droite), donc d’axe vertical, que dans le plan vertical (haut ou bas), d’axe horizontal. Les proportions ont été choisies pour que les résistance aux déformations d’axe vertical soient exactement le double de celles d’axe horizontal. Il en est donc de même du moment quadratique. On peut le vérifier avec :
\(Q\)/axe horizontal \(= L \times l^3/12 = l \sqrt{2} \; l^3/12 = l^4 \sqrt{2} /12\)
\(Q\)/axe vertical \(= l \times L^3/12 = l \times (l \sqrt{2})^3/12 = 2 l^4 \sqrt{2} /12\)
Comment les représenter ? Par des segments d’origine \(G\), centre de gravité de la section dans la direction et le sens des vecteurs \( \normalsize \overrightarrow{MtR/M}\), opposés aux vecteurs \(\overrightarrow{MtF/M}\). Du fait des propriétés du produit vectoriel, les valeurs de \(Q\) se représentent dans la direction de l’axe des déformations et non dans le plan des déformations : le moment quadratique qui résiste aux courbures dans le plan vertical se représente horizontalement ! Aïe ! J’ai renoncé à changer de convention. Cela m’aurait obligé à un commentaire explicatif à chaque utilisation.
Moment quadratique et moment d'inertie ?
Dans l’exemple précédent, la section rectangulaire qui résiste à la flexion est une surface. Supposons qu’on lui donne une épaisseur \(e\). Elle devient alors un objet, une plaquette, dotée d’une certaine masse surfacique \(\rho_A\) (rhô A) en Kg/m² qui dépend du matériau et de \(e\). Imaginons cette plaquette munie d’un axe passant par son centre de gravité, axe pour l’instant contenu dans son plan[3]Note [3] – Si l’axe de la plaquette passant par G n’est pas astreint à rester dans son plan, les valeurs du moment quadratique sont limitées par l’enveloppe d’un volume : l’ellipsoïde d’inertie., autour duquel la plaquette peut tourner, comme une toupie. Cette toupie présentera une résistance à la mise en rotation différente selon la direction de l’axe (mais identique pour un sens ou l’autre de rotation autour de cet axe, comme les résistances aux flexions dans un sens ou l’autre). C’est cette résistance à la mise en rotation qu’on appelle son moment d’inertie.
Ce qui caractérise la résistance à la mise en mouvement du centre de gravité d’un corps c’est sa masse.
Ce qui caractérise la résistance à la mise en rotation d’un corps autour d’un axe passant par son centre de gravité c’est son moment d’inertie.
Ce moment d’inertie de la plaquette dépend de la forme et des dimensions de sa surface par une grandeur \(I\) et de sa masse surfacique \(\rho_A\) (rhô A) en kg/m². Moment d’inertie = \(I \times \rho_A\).
\(I\) est égal au moment quadratique de la surface, avec des valeurs distribuées selon les rayons de la même ellipse.
Est-ce surprenant que la même grandeur intervienne dans des phénomènes complètement différents : résistance à la flexion d’une surface et résistance à la mise en rotation d’une plaque ? Cela s’explique facilement par le fait que pour l’un ou l’autre de ces phénomènes, un élément de surface intervient par le carré de sa distance à l’axe de flexion ou axe de rotation.
Si \(I\) moment quadratique en m4
Résistance à la flexion d’une section = \(I \times y\) (module de Young en N/m²)
Résistance à la mise en rotation d’une plaque = \(I \times \rho_A\) (rhô A masse surfacique en kg/m²)
La résistance à la mise en rotation d’un solide s’appelle son moment d’inertie. Par abus de langage la résistance à la flexion peut aussi s’appeler moment d’inertie mais le terme “Moment quadratique” est plus précis : il rappelle la puissance 4 aussi j’ai privilégié son usage. Quant à l’ellipse qui renseigne sur ses valeurs suivant l’axe de déformation le terme usuel est ellipse d’inertie qui entretient la confusion ! C’est même évoqué dans Wikipédia : « Le moment quadratique est encore très souvent appelé moment d'inertie. Cependant, bien qu'il présente de claires similitudes, il ne rend compte que de la géométrie d'une section et non de sa masse. » Qu’y faire ? D’autres langues ont peut être une terminologie plus précise ?
Pire encore ! Les recherches sur les cannes à mouche sont doublement exposées à ces confusions car les causes des flexions de la canne sont liées au moment d’inertie de l’ensemble {Canne ; Soie} alors que les résistances à ces déformation sont, ponctuellement, les résistances à la flexion de ses sections !
06 mai 2020
Le rayon de courbure est proportionnel à la résistance à la flexion et inversement proportionnel au moment fléchissant.
Un élément d’une tige cylindrique de rayon \(r\) de longueur \(L\) qui est soumis à un moment de flexion \(MtF\) va se courber jusqu’à ce que les fibres étirées ou tassées exercent un moment qui équilibre \(MtF\). \(I\) est le moment d’inertie de la section, c'est-à-dire sa résistance à la flexion, \(I=k \times r^{4}\) (\(k\) rassemblant les caractéristiques géométriques et le module de Young du matériau).
\(R\) est le rayon de courbure \(OG\) (\(G\) est le centre de gravité de la section - Voir schéma)
\(R\) est proportionnel à \(I\) et inversement proportionnel à \(MtF\).
\(R= \displaystyle \frac{I} {MtF} = \displaystyle \frac{k \times r^4} {MtF} \; \) (*)
On s'intéresse à la contrainte \(c=\displaystyle\frac{dL} {L}\) des fibres extérieures.
Les fibres passant par \(G\) conservent leur longueur \(L\).
\(\alpha\) est l’angle en radian de centre \(O\) qui intercepte l’arc de longueur \(L\).
$$L=R \times \alpha$$
\(L'\) est la longueur de la fibre extérieure : \(L'=(R+r) \times \alpha\)
\(dL=L'-L=(R+r) \times \alpha-R \times \alpha=r \times \alpha\)
d'où : \(c=\displaystyle \frac{dL} {L} = \displaystyle \frac{r \times \alpha} {R \times \alpha} = \displaystyle \frac{r} {R} = r \times \displaystyle \frac{1} {R}\)
Comme \(R=\displaystyle \frac{kr^4} {MtF} \; \)(*), on a : \(\displaystyle \frac {1} {R} = \displaystyle \frac{MtF} {kr^4}\) $$c= \frac {dL} {L} = r \times \frac{MtF} {kr^4} = \frac{MtF} {kr^3}$$
Si la tige est soumise à des moments de flexion variables en différents points de sa longueur, l’égale contrainte impose la conservation de ce rapport.
et de \(\displaystyle \frac{MtF} {kr^3} =c \;\) découle \(\; r= \displaystyle \sqrt[3]{\frac{MtF} {ck}}\)
L’égale contrainte impose que le rayon \(r\) de la tige soit proportionnel en tout point à la racine cubique du moment fléchissant. |
(Exemple : si \(MtF\) est multiplié par 8, le rayon \(r\) doit être doublé : \( \sqrt[3]{8} =2 \) )
Ce résultat est valable pour toute section, et toute dimension qui la définit, en particulier pour une section hexagonale et sa cote sur plats.
J’ai été moi-même surpris par les résultats : à section égale (il est bon de le répéter) le moment quadratique de la section en triangle équilatéral est supérieur à celui du carré, lui-même supérieur à celui de l’hexagone ! Moins il y a de côtés plus la résistance à la flexion augmente, toutefois pas dans des proportions énormes. La preuve faite de la meilleure “performance” de la section en triangle équilatéral vient justifier à posteriori mon choix pour des renforts “à minima ” dans les assemblages en biseaux (le chapitre « Assemblage par épissures » leur est consacré).
Section | T. équilatéral | Carré | Hexagone | Disque |
\(I=k\times{A^2}\) exact | \(I=\displaystyle \frac{\sqrt{3} } {18}\times{A^2}\) | \(I=\displaystyle \frac{1} {12}\times{A^2}\) | \(I=\displaystyle \frac{5\times\sqrt{3}} {108} \times{A^2}\) | \(I=\displaystyle \frac{1} {4\pi} \times{A^2}\) |
\(k\) approchée | 0,0962 | 0,08333 | 0,0802 | 0,0796 |
\(\displaystyle \frac{R} {r}\) (voir 3) | 2 | \(\sqrt{2}=1,414..\) | \(\displaystyle \frac{2} {\sqrt{3}} =1,115\ldots\) | 1 |
Il y a une contrepartie car un autre phénomène entre en jeu. C’est une question de contraintes : plus les fibres extérieures sont éloignées du centre de gravité \(G\) plus elles sont étirées ou compressées en flexion. Pour nos sections polygonales les fibres extérieures les plus éloignées de \(G\) sont celles qui sont aux sommets, leur distance à \(G\) est le rayon \(R\) du cercle circonscrit, et les moins éloignées sont aux milieux des côtés, à une distance de \(G\) qui est le rayon \(r\) du cercle inscrit.
Dans un triangle équilatéral \(R = r \times 2\), dans le carré \(R =r \sqrt{2} \;(r \times 1,414\ldots)\), dans l’hexagone \(R=r \times \displaystyle \frac{2} {\sqrt{3}} \;(r \times 1,115\ldots)\).
Donc l’augmentation de la résistance à la flexion quand on diminue le nombre de côtés se fait au détriment d’un déséquilibre accru des contraintes des fibres extérieures. Concernant la section circulaire des cannes en fibres, qu’on peut considérer comme un polygone avec une infinité de côtés, elle est la moins efficace en résistance à la flexion mais elle assure l’égalité stricte des contraintes des fibres sur la périphérie. Il n’y a pas de direction de flexion qui augmente les risques de rupture. On peut la qualifier d’isobare.
Remarque sur les tiges et troncs des végétaux. Il est intéressant de constater que les hasards des mutations ont produit des tiges végétales de sections polygonales diverses : celles des carex sont le plus souvent triangulaires, celles des lamiacées sont quadrangulaires proches du carré, celles des cucurbitacées pentagonales, etc. mais qu’une majorité est de section circulaire, pleine ou creuse comme les graminées, et en particulier les bambous. Le fait de n’avoir pas de risque de rupture augmenté dans une direction de flexion, l’homogénéité des contraintes périphérique est certainement une des raisons de la prépondérance de cette disposition des tiges végétales.
11 avril 2020
La méthode simple que je propose est valable pour toute section, pleine ou creuse.
Elle permet de quantifier à masse égale le gain en résistance à la flexion ou, à résistance à la flexion égale, de quantifier l’allègement.
Il faut disposer des caractéristiques module d’élasticité (ou de Young) \(E\) et masse volumique \( \large\rho\) (rhô) des deux matériaux \(A \:et\: B\) à comparer.
On calcule les rapports \( \Large\frac {E} {\LARGE\rho^2}\) pour \(A \:et\: B\). On obtient \(K_A \) et \( K_B\).
La plus grande valeur des deux décide du matériau qui résiste le mieux à la flexion. Le rapport \(F\) du plus grand sur le plus petit renseigne sur le gain de résistance à la flexion à masse égale.
Le rapport d’allègement \(L\) à résistance à la flexion égale est à la racine carrée de l’inverse de \(R\: \) : \( \:L = \sqrt{R^{-1}} \:=\:\sqrt{\frac{1}{R}} \ \) ou \(\large\frac{1}{\sqrt{R}}\)
C’est plus facile à faire qu’à dire. Exemple avec deux alliages métalliques, de l’acier “à ressorts” et du duralumin. S’ils ne sont pas utilisés pour les cannes à mouche leur exemple est intéressant.
acier | duralumin | |
Module d'élasticité | 220 GPa | 75 GPa |
Masse volumique | 7 800 kgm⁻³ | 2 700 kgm⁻³ |
Kacier = 220 x 10⁹ / 7 800² = 3 616,04
Kduralumin = 75 x 10⁹ / 2 700² = 10 280,07
Ces indices sont en Nm⁴kg⁻² mais c'est sans importance pour la suite.
C’est donc le duralumin qui est le plus résistant à la flexion à masse égale.
Dans quelle proportion ? \(F= \large\frac{10\:280,07}{3\:616,04} \normalsize =2,8\ldots\) Le duralumin résiste 2,8 fois plus à la flexion que l’acier à masse égale.
À résistance à la flexion égale quel allègement procure le duralumin par rapport à l’acier ? \(L = \sqrt{1/2,8}= 0,5928\) ce qui correspond à un allègement de l’ordre de 40 %. On comprend son usage dans l’aviation.
Il faut remarquer que la masse volumique intervient par son carré dans le calcul de \(K\) alors que l’idée qui vient immédiatement à l’esprit est de comparer les rapports \( \Large\frac {E} {\LARGE\rho}\). Ce serait juste dans le cas d’un étirement. Si l’exemple est intéressant c’est parce que, dans ce cas, l’acier l’emporterait de peu. Les critères de choix diffèrent si la pièce est soumise à un étirement ou une flexion.
Il n’y a pas à douter que les coefficients \( \Large\frac {E} {\LARGE\rho^2}\) des fibres de carbone (il y a plusieurs qualités ou grades) sont largement supérieurs à celui du bambou. Leurs masses volumiques sont voisines du double mais ce handicap est mieux que compensé par l’augmentation du module de Young. De plus, la structure tubulaire améliore les performances. Pour les fibres de carbone, les rapports \( \Large\frac {E} {\LARGE\rho^2}\) permettront d’évaluer l’avantage d’un grade par rapport à l’autre à condition que les coefficients de creusement Dext./Dint. soient égaux.
Et pourtant les cannes en bambou fonctionnent bien, et longtemps. À l’avantage du bambou plein, ou mieux alvéolé, il y a l’absence d’ovalisation de la section quand la canne est courbée. Un autre avantage et non des moindres c’est de pouvoir tailler des profils avec des pentes variables, et même très variables si l’on suit mes calculs quand on arrive en pointe de scion. C’est quasiment impossible à réaliser avec une nappe de fibres roulée sur un mandrin. Il n’en reste pas moins qu’il est difficile de rater une canne en fibre de carbone. Ce matériau tolère les longueurs excessives qui obligent à multiplier les brins et les emmanchements pour des questions d’encombrement. Alors qu’avec le bambou, les cannes sont vite lourdes et fatigantes si l’on n’a pas une distribution précise des épaisseurs et une juste longueur. Gare si on néglige de traquer les faiblesses ou poids morts : les erreurs de conception se révèlent crûment ! Également, comme il permet de construire une canne « de A à Z » avec un outillage relativement simple, c’est le matériau idéal pour un chercheur.
La possibilité d’envoyer à plus de vingt mètres une masse de l’ordre du décigramme ne relève pas de la magie mais des lois générales de la physique. En l’occurrence du principe de conservation de l’énergie cinétique de la ligne.
Lors d’un lancer avant bien réussi, la ligne, au moins à la fin de sa propulsion, ne doit pas présenter d’ondulation et se comporte comme une masse unique animée d’une vitesse \(V_0\) en m/s. Elle possède une certaine énergie cinétique \(E_c = ½ M_s {\large V}_0^{2}\). Puis la canne retient la ligne et une boucle se forme, la masse de la partie mobile diminue, ce qui impose que la vitesse augmente. Dans la suite on considère que le fil est homogène et que sa masse est proportionnelle à sa longueur.
Un exemple : si l'on a lancé 16 m d’un fil homogène à la vitesse de 5 ms-1, quand il ne reste plus que 4 m mobiles (12 m étant immobilisés) la division par quatre de la masse mobile impose, pour conserver l’énergie cinétique, le doublement de la vitesse qui passe à 10 ms-1. Et quand il ne reste plus qu’un mètre en mouvement (15 m étant immobilisés), cette nouvelle division par quatre de la masse mobile impose un nouveau doublement de la vitesse qui passe à 20 ms-1 ( à noter que cette accélération serait augmentée avec un fil conique).
On conçoit que, la masse mobile tendant vers zéro, la vitesse tende vers l’infini. Une bonne image est de considérer la ligne comme un tube contenant un gaz que le pincement dû à la boucle repousse dans la seule partie mobile. Comme il est de plus en plus comprimé il ne peut qu’exploser à la fin. C’est le claquement du fouet que certains expliquent par le passage du “mur du son” de sa mèche. Cette idée a même fait l’objet d’une question au baccalauréat en 2012 !
Qu’en penser ? Mais déjà qu’est-ce que le “mur du son” ?
Pour un avion, l’énorme énergie dégagée par la combustion du carburant se disperse dans l’air sous la forme de chaleur et de vibrations violentes des gaz. C’est le bruit ou plutôt le vacarme de l’avion qui se propage autour de lui à la vitesse du son, voisine de 300 m/s. Quand l’avion atteint cette vitesse, il rattrape l’énergie qui s’est propagée devant lui, qui s’accumule et finit par se dégager brutalement sous la forme d’une explosion.
Alors notre soie rattraperait-elle son énergie sonore ? A l’évidence, sous réserve des frottements de l’air, des pertes d’énergie dues à l’élasticité du fil, à sa résistance à la flexion ou à son effilochement, la vitesse de la mèche peut en théorie dépasser celle du son. Mais cela n’implique en rien que le claquement résulte d’un passage de son “mur”. En fait le bruit qu’on entend est du même ordre qu’un claquement de porte ou de nos mains quand on applaudit. L’énergie cinétique de la porte ou de nos mains passe à zéro en un temps très court et il faut bien qu’elle s’échappe en ébranlant les murs et l’air. Cette énergie qui doit s’évacuer en un temps très bref explique pourquoi une gifle ou un coup de fouet sont si douloureux. Donc oui pour l’extrême vitesse, mais le bruit n’a rien à voir, ni à entendre, avec le mur du son !
Dans notre pratique de pêche à la mouche, c’est l’accumulation de l’énergie cinétique en pointe qui assure au bas de ligne une vitesse suffisante pour qu’en dépit de sa légèreté il puisse vaincre les frottements de l’air et se déployer. Vitesse bien supérieure à celle de la pointe du scion à la fin de sa propulsion. C’est pourquoi il est si difficile de lancer seulement le bas de ligne. Il faut que la canne elle-même soit capable de se déplacer très vite, ce qui pose le problème de son inertie propre, de la légèreté de la pointe du scion et en particulier de celle de l’anneau de tête. D’une façon générale, plus le lancer est court plus faible est la force à exercer sur la ligne mais plus grande est la vitesse à lui communiquer.
Quant au bas de ligne, sa mise au point consiste à doser épaisseurs et longueur (encore une question de profil !) pour qu’il puisse s’étendre et que la mouche se pose sans frapper l’eau. Le bas de ligne et la mouche servent d’échappement pour l’énergie cinétique. Le problème est un peu différent en nymphe car le leurre se comporte comme un projectile et c’est son inertie qui permet d’étendre la partie la plus fine du bas de ligne (10 centièmes, 8 centièmes...)
Fonction horaire du déploiement de la ligne.
Indépendamment de toute l’énergie qui est perdue pour des raisons mécaniques dans le fil, et dans les frottements de l’air, en considérant que la boucle à une “épaisseur” nulle, j’ai trouvé intéressant de rechercher la fonction horaire qui relie la durée \(t\) en seconde avec la position \(x\) en mètre soit de l’extrémité libre du fil, soit du “front de la boucle”.
En retenant cette dernière possibilité :
\(L\) est la longueur du fil homogène en m, \(V_0\) la vitesse initiale de la boucle (qui est la moitié de celle de la soie).
\(x\) est la position du coude ou front de la boucle :
\(x=L - \left(L^{1,5}-3/2\;t\; V_0\sqrt{L} \right)^{2/3} \) |
Voir le détail des calculs ici
Un exemple avec \(L\)=16 m \(V_0\)= 4 m/s
\(x=16-\left(64-24\;t\right)^{2/3} \)
La durée de déploiement du fil est de 8 s/3. Si on veut la position de l’extrémité libre de la ligne qui parcourt pendant la même durée 32 m, il suffit de doubler \(x\).
Les valeurs de \(t\) se succèdent d’abord tous les 1/3 s puis à partir de 7/3 s avec un pas de 1/24 s
t | 1/3 | 2/3 | 3/3 | 4/3 | 5/3 | 6/3 | 7/3 | 57/24 | 58/24 | 59/24 | 60/24 | 61/24 | 62/24 | 63/24 | 64/24 |
\(x\) | 1,36 | 2,79 | 4,30 | 5,92 | 7,683 | 9,65 | 12 | 12,34 | 12,704 | 13,08 | 13,48 | 13,92 | 14,41 | 15 | 16 |
\(2x\) | 2,72 | 5,58 | 8,61 | 11,84 | 15,36 | 19,30 | 24 | 24,68 | 25,404 | 26,16 | 26,964 | 27,84 | 28,82 | 30 | 32 |
Ci-dessous le graphique sur lequel on peut vérifier que la vitesse instantanée du front de la boucle pour \(t=0\;s\) est 4 m/s et que pour \(t=7/3 \;s\), \(x=12\;m\), la masse mobile du fil étant divisée par 4, la vitesse a doublé en passant à 8 m/s.
Durée du déploiement : un tiers de gagné !
Si \(V_S\) est la vitesse initiale de l’extrémité de la soie qui doit parcourir une distance double de la longueur \(L\) de la soie, s’il n’y avait pas d’accélération, la durée de déploiement serait \(2L/V_S\). Elle est en fait raccourcie du 1/3 ! \(T_D=4L/3V_S\) (au lieu de \(6L/3V\))
Ou, si on considère la boucle qui se déplace de \(L\) avec une vitesse \(V_B\) qui est la moitié de \(V_S\;\), \(T_D = 2L/ 3V_B\) (soit un tiers de moins que \(3L/3 V_B\)).
Il faut bien retenir que les calculs qui précèdent sont purement théoriques, puisque toutes les causes de pertes d’énergie sont négligées. Il n’empêche qu’ils permettent de saisir la réalité du principe du fouet.
Pourquoi la soie ne tombe pas ?
Une dernière explication : pourquoi le fil ne tombe-t-il pas quand il se déploie ? Parce qu’il est tendu par la force nécessaire au “freinage” des éléments du fil qui s’immobilisent quand ils passent de la partie mobile à la partie fixe de la boucle. Pour la calculer, il faut considérer l’accélération \(\large \gamma\) de la partie mobile qui s’obtient par la dérivée seconde de la fonction horaire et la masse de cette partie mobile puis appliquer \(F=M \large \gamma\)
Pour calculer cette force, il faut considérer la boucle comme une roulette virtuelle de très petit diamètre qui transmet à la partie mobile de la ligne la force d’intensité \(F\) nécessaire pour lui communiquer une accélération \(\large\gamma\)
Cette accélération de la partie mobile s’obtient par la dérivée seconde de la fonction horaire \(x= f(t)\). La masse \(M\) de la partie mobile se déduit aussi de la fonction horaire. Il suffit ensuite d’appliquer la loi fondamentale de la dynamique \(F=m\large\gamma\). Le détail des calculs est disponible sur demande.
On obtient, avec \(t\) en secondes, la masse de soie \(Ms\) en kilogramme, la longueur de la ligne \(L\) en mètres, \(V_0\) la vitesse initiale de la ligne en \(m.s^{-1}\), \(F\) en newton l’intensité de la force qui accélère la partie mobile et tend la partie fixe de la ligne :
\(F=\dfrac{M_s \times V_0^{2}}{2} \times \left( 2^{1,5} L^{1,5} - \dfrac{3V_0L^{0,5} \times t}{2^{0,5}}\right)^{-\Large\frac{2}{3}}\)
Cette force, comme la vitesse de la partie mobile de la ligne, tend vers l’infini. Heureusement qu’il y a de nombreuses causes de pertes d’énergie !
Les pertes d'énergie en cours de lancer.
Le fonctionnement des cannes à mouche, le déploiement de la ligne, ont été abondamment étudiés aux US, semble-t-il dans toute leur complexité. C’est comme si, concernant la chute des corps, tous les paramètres étaient pris en compte, depuis la forme de l’objet à la température de l’air, à la poussée d'Archimède, et jusqu’à la force de Coriolis ! A tel point que la loi sur la chute libre risquerait d’être occultée. En tout cas c’est ce qui m’apparaît dans les études qui nous intéressent, impression sans doute aggravée par ma méconnaissance de la langue. Je n’ai pas trouvé de trace de la fonction horaire \(x=L - \left(L^{1,5}-3/2\;t\; V_0\sqrt{L} \right)^{2/3} \) dont j’ai répété qu’elle décrivait exactement le déploiement de la soie, mais à condition que toutes les perturbations soient exclues.
Ceci étant, quelles sont-elles ?
D’abord les pertes d’énergie cinétique dues à la ligne elle même si elle s’allonge sous la traction. Également sa résistance à la flexion, car la boucle en cours de déploiement se déplace, ce qui fait que toutes les parties de la ligne ont été fléchies successivement. Enfin et surtout les frottements de l’air.
Comment minimiser ces pertes : avec une ligne qui s’allonge le moins possible, telles les soies naturelles (comme déjà dit dans « Études de profils »), avec la ligne la plus souple possible en flexion, on dit sans mémoire, enfin avec la ligne la plus dense possible pour, à masse égale, diminuer le diamètre donc le “maître couple” ce qui diminue la traînée. Mais on est limité si on veut que la ligne reste flottante, même si la tension superficielle y contribue si on la graisse. Le lanceur a son rôle à jouer en réduisant le “maître couple” avec une boucle serrée ce qui se réalise automatiquement avec les « waves action » mais est possible avec n’importe quelle canne.
Une question demeure : le rôle de la pesanteur. Évidemment, sans pesanteur ni frottements de l’air, la soie ne s’arrêterait pas !
J’ai expliqué dans le paragraphe précédent ce qui l’empêchait momentanément de tomber en cours de déploiement. Allons plus loin : un objet qui monte perd de l’énergie cinétique et gagne une énergie potentielle (qui peut être rendue) ; et inversement quand il descend. Ce que le lanceur peut exploiter malgré la faible variation de hauteur de la soie au cours du lancer en adoptant une trajectoire de déploiement de la soie légèrement montante vers l’arrière. Voilà le schéma du mouvement de l’extrémité de la ligne suivant l’arraché (quand on fait décoller la soie posée sur l’eau) lors d’un faux lancer sans allonger le fil :
.